如何整体衡量精益生产实践成果
本文来源于帆软数据应用研究院,原创文章,作者:者宇飞,发布于 《中国信息化杂志》(2021年第1期)。转载请注明出处、作者和本文链接,违规转载法律必究。投稿或合作请微信联系【商业智能研究】公众号。
近年来,随着精益生产概念的引入,大部分制造业开始争相学习这种生产模式。在起初一到两年的实践过程中,在成本层面会有部分减少,但是在第三年左右开始,虽然依旧存在改善的点,但其成果无法在财务层面直观呈现,精益生产模式的导入也不得不在此中止。很多时候我们不得不质疑,这种生产模式是否真的契合自己的企业,或者说这种概念只是徒有其表。
一、浅析精益生产模式及其实践现状
1、何为精益生产模式
精益生产前身为丰田模式,这种模式是当时丰田为应对美国大批量生产模式、基于自身国情及市场而探索出的成果,其最初的核心主旨为:不用担心钱的问题,缩短过程时间是丰田的原则。渐渐迭代为如今由准时化及自动化两大支柱构成的精益生产模式,而践行精益生产模式的企业即为精益企业,如下图所示:
2、制造业现状解析
无论对于制造业还是绝大多数的企业来说,核心的目标均为:降本、提质、增效。而三者的权重及实践路径并没有被完整定义,相互之间也并没有进行数据的串通,大部分企业的经营发展及内部绩效的评定依旧由纯财务数据支撑。虽然财务数据的衡量具有绝对的标准型及成果可视性,所达成的结果我们称之为:局部最优,但其弊端也会逐渐显露。
何为局部最优?在这里我们举一个简单的例子:当“降本”作为企业的经营重心时,分发给各业务部门的指标也不尽相同。对于采购部而言,以更低的价格采购物料便为其目标,而在同供应商谈判的过程中,提高采购量即是最有效的降价途径;对于生产部门来讲,减少换线次数,采用大批量生产的模式,其生产成本也会大幅下降;再比如对于销售部门而言,实施大批量销售,降低销售费用也是最具有可行性的降本措施。
以上种种行为的结果自然是每个部门的财报中都会体现相应改善行为在降本层面做出的卓越贡献,而大批量的雏形也在此时开始浮现,库存的增加,产品的周转减慢,而各个现场依然会继续进行“降低进价”、“简化生产工序”、“寻找便宜的仓库”,持续推进完全独立的、局部最优的降本活动。最终,各部门的成本降低了,但从公司整体来看,原材料仓、半成品仓、成品仓的增大,物流周期的拉长,大订单的不稳定性增加,种种情境会导致企业内部出现巨大的损失。
3、精益生产的推进困境
正如我们在文初所提到的,精益生产的理念在初步引入企业内部时,确实会在成本层面有部分成果。但当我们仅局限于成本层面,由此点出发去套用精益理念时,其结果也同改善前的状态如出一辙。
其实精益生产的改善方式其出发点绝非成本,而是通过自动化在确保质量的基础上,彻底实现缩短过程时间,进而带来收益。
所谓过程时间,在财务层面又如何去量化,才能体现出企业在实践精益生产过程中的变革,得到高层的认可以继续推行该种生产模式。这时候我们就需要引入新的指标,新的“X轴”——时间。
二、“时间“之于”赚钱能力“——收益性
1、库存的收益性损失
低库存始终为贯穿精益生产理论的生命线之一,制造型企业也在大力推动降低库存的措施,而后者往往会直接通过现金流的稳定性及库存转化为资金后的利息损失,来衡量库存健康程度,其关注的指标通常为库存周转率及呆料在仓天数,而长期持有库存会给客户带来什么样更深层次的风险,即“一万元的库存停留一天,会带来什么样的损失”,我们始终缺乏一个明确且细粒度的指标来衡量。
在这里我们引入一个小场景来细化一下何为收益性。
假设有四辆库存单价为10W的小轿车准备发往某处经销商,一辆单趟运输成本为5000的货运车容量为5辆小轿车,而还有一辆小轿车将于第二天生产完毕。这个时候我们都会选择第二天将五辆汽车同时运走,因为此时会降本5000/4-5000/5=250。
而精益生产的前身——丰田生产则是无条件缩短过程时间,即第一天将四辆汽车运走。可能在传统会计思维下我们无法理解这种行为,这里我们引入新的指标:库存毛利率=每年产生毛利/库存/365,即假设公司不会让库存停留,每一天都在赚钱,此时一万元的库存每天会带来多少的收益,反之库存多积压一天便会少赚相应的钱。
利用这个公式我们回到前面的问题,丰田08年的年库存毛利率为806%,也就是每1w的库存,工作一年可以赚到80627元,即一天可以赚到221元,而如果多保有一天库存,就会有221元的损失,那么此时我们让题目内的车多停放一天,相当于损失8840元。此时我们将250元同8840元相比,便可以看出两种方式下丰田为什么会选择无条件缩短过程时间。不过需要指出的是,在库存层面,收益性指标的价值在于放大库存的积压问题及实行相应改善后的结果反馈。
2、速度同金钱的衡量法则——收益性恶化率
在运输层面,传统模式我们都会选择为降低成本而选择运输费最低的物流方式,但是,那些高昂的、快速的运输方法必然有其存在的意义。结合精益生产我们知道加快物流速度,库存就会减少,这也是我们需要改善的点,但是结合实际情况,企业具体应该在运费上多支出一些,以实现快速运输,还是多花一些时间减少运费支出,此时相关人员很难做出正确的判断,这个时候我们将物流后出售收益性及公司门口(不存在物流)收益性恶化率对比,,进而判断收益性恶化最低的方案。
收益性恶化率=(1-运费比)/(1+过程时间比);
其中,运费比=运费/毛利;
过程时间比=运输过程时间/制造过程时间;
可以看出,商品的毛利越高,运费对收益性恶化率的影响越小。再比如像粮食这种需要至少半年才能收获的产品,运输时间达到30天也不会有过大的影响,而制造业目前基本在两个月内就可以完成生产,这意味着分母变成了1.33,而我们推进改善,减小库存,便可以与物流相同的20天完成生产,这样分母就变成了2.0,收益性恶化率降到了一半以下。
同样,我们可以利用此公式计算比较外企选择在中国生产以及本土生产的收益性恶化率,在算上运费及运输过程后,反而有些情况在中国使用较为实惠的劳务费却不如在本土生产。
3、企业整体收益能力评价
之前两个指标我们是对现场改善结果进行评价,那么如果从全局即企业整体评价出发,如果经由财务分析,对准时化进行评价,才能真正体现企业的实践成果。
这里我们首先引入资本利润率的指标,财务层面我们常常以这个指标出发衡量企业收益率,但是它所设计的指标:利润总额、本期净利润、总资本指标等,无法直接反应生产现场的实力,而更大部分的受该企业财务效率以及债券回收能力的影响。
在这里我们需要将其公式进行进一步的改造:
收益性评价指标 = 销售总利润/存货金额
=(销售总利润/销售成本)*(销售成本/存货)
=(销售成本利润率)*(库存周转率)
需要说明,这里为什么不使用销售额/存货来表示库存周转次数,因为如果有的企业销售额会员高于销售成本,此时并不能真实反馈现场改善而带来的收益能力。
这里得出的收益能力可分解为总部所应负责的销售成本利润率以及在生产、物流现场通过缩短过程时间以及实现准时化生产的库存周转率。
三、精益生产实践之路探索
前面讲到全局最优并非局部最优的结果导向,而目前在生产和销售新商品时,很多情况下我们会引入成本企划,即由丰田流出的成本管理手法。这种办法首先时设定利润,然后推算成本,即所谓的目标成本,然后依次拆解给各部门需要削减的成本金额,从而进行改善活动,但是正如局部最优的一般客观性结果来说,各部门的单元化改善行为,往往与成本企划的预期目标背道而驰。
那么具体应该怎么去执行以及监测,这个时候我们应该跳出传统的成本思考范畴,选择前文所提到的收益性,其单位为元*天,即以缩短过程时间为重心进行思考改善。无论从采购、销售、生产角度,对相应的时间也要进行更详细的交涉,依次考虑对于收益性的影响。
结语
就多数离散制造企业来说,精益生产的理念其实已经融入于现场之中,只是在财务层面缺乏更细粒度的指标来衡量其改善结果,同时在改善层面也因繁琐的审批流程及制度将改善点以惰性覆盖。因此,一定要将“现在是最好的,现在就是好的”想法摒弃,彻底作好自动化,不断追求准时化以获得最大收益。
相关文章推荐
关注帆软数据应用研究院公众号,获取更多内容

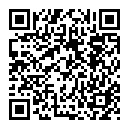